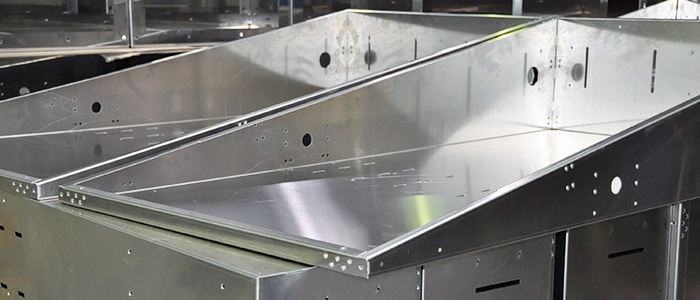
MECHANICAL PRODUCTION
CNC punch laser, deburring/straightening, bending, turning & milling, pressing, welding & grinding, painting, screen printing, pickling & passivation, soldering
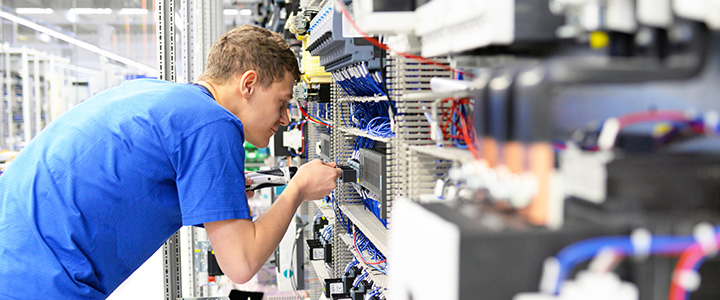
ASSEMBLY
Mechanical assembly
Electrical assembly with ESD protection area & test bay